Discover The Simple Solution To Improving Your Skew Correction Process
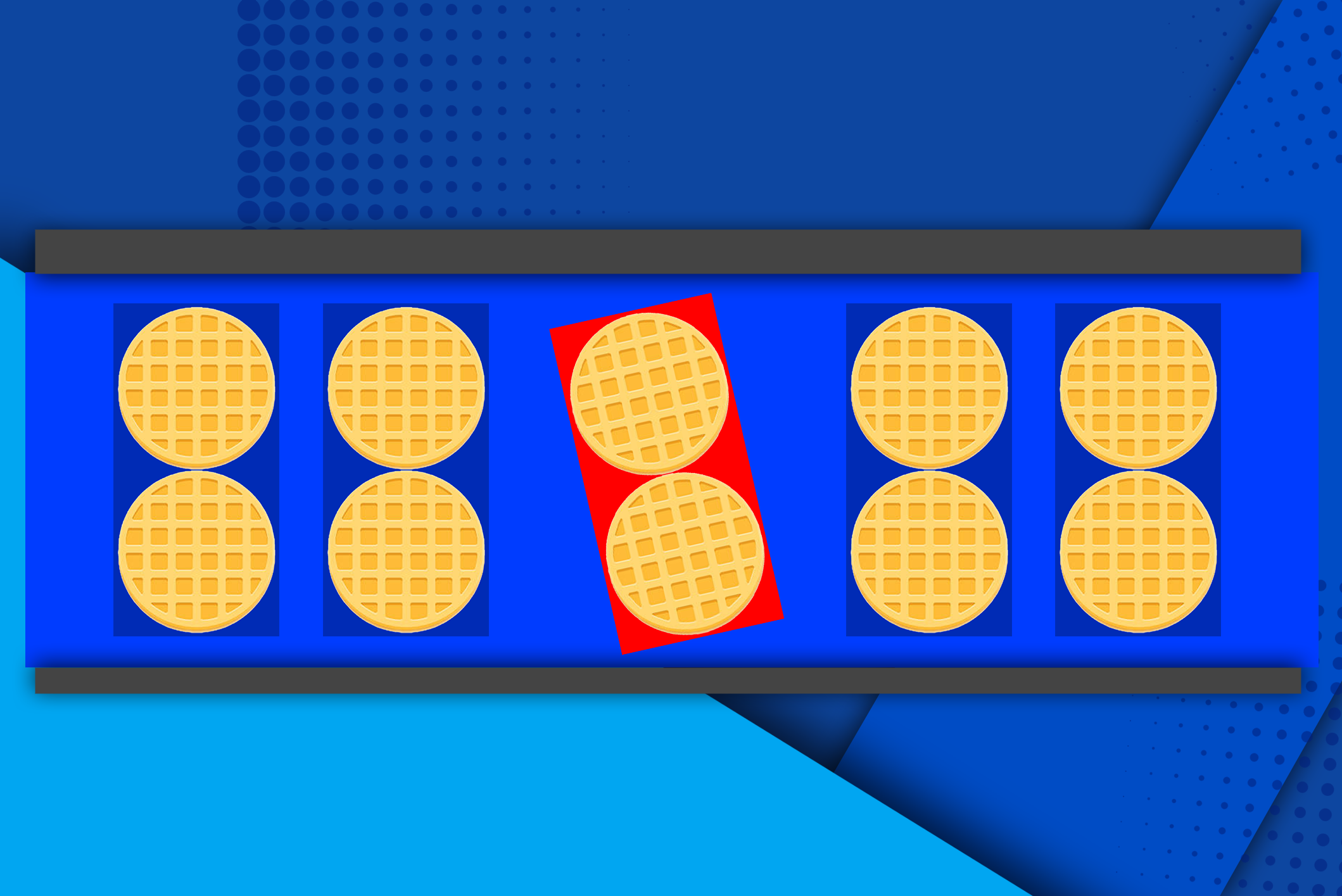
Why Your Skew Correction Process Is Likely Flawed (And How To Fix It)
When packaging a product, skew correction often plays an important role. It is an area, that if well optimized, can have a dramatic impact on the speed and efficiency of your process.
Many factories unknowingly have an over-complicated method in place for achieving skew correction that is driving down profits.
What is Skew Correction?
Before we dive in, let’s make sure we’re all on the same page. If you are unfamiliar with the term, skew correction is exactly what it sounds like: taking product that is skewed on a belt and correcting it so that it is in proper position (often, just before being packaged).
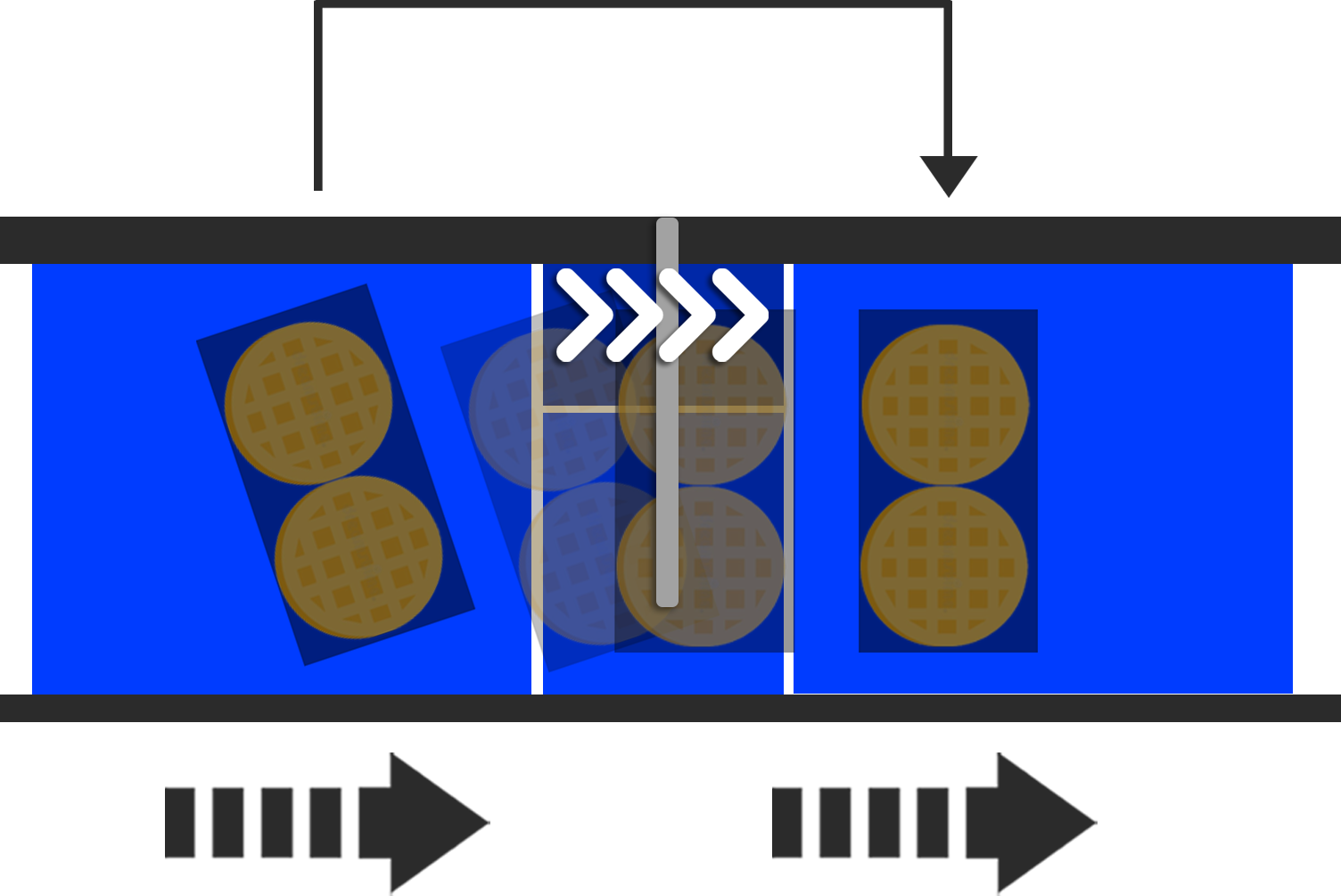
This is traditionally done using one belt feeding skewed product onto another belt. That belt will then use a “bumper” to push up against the product, correcting the skewed product.
To transfer the product from one belt to the other, an incline might be used to “toss” the product onto the belt performing the skew correction.
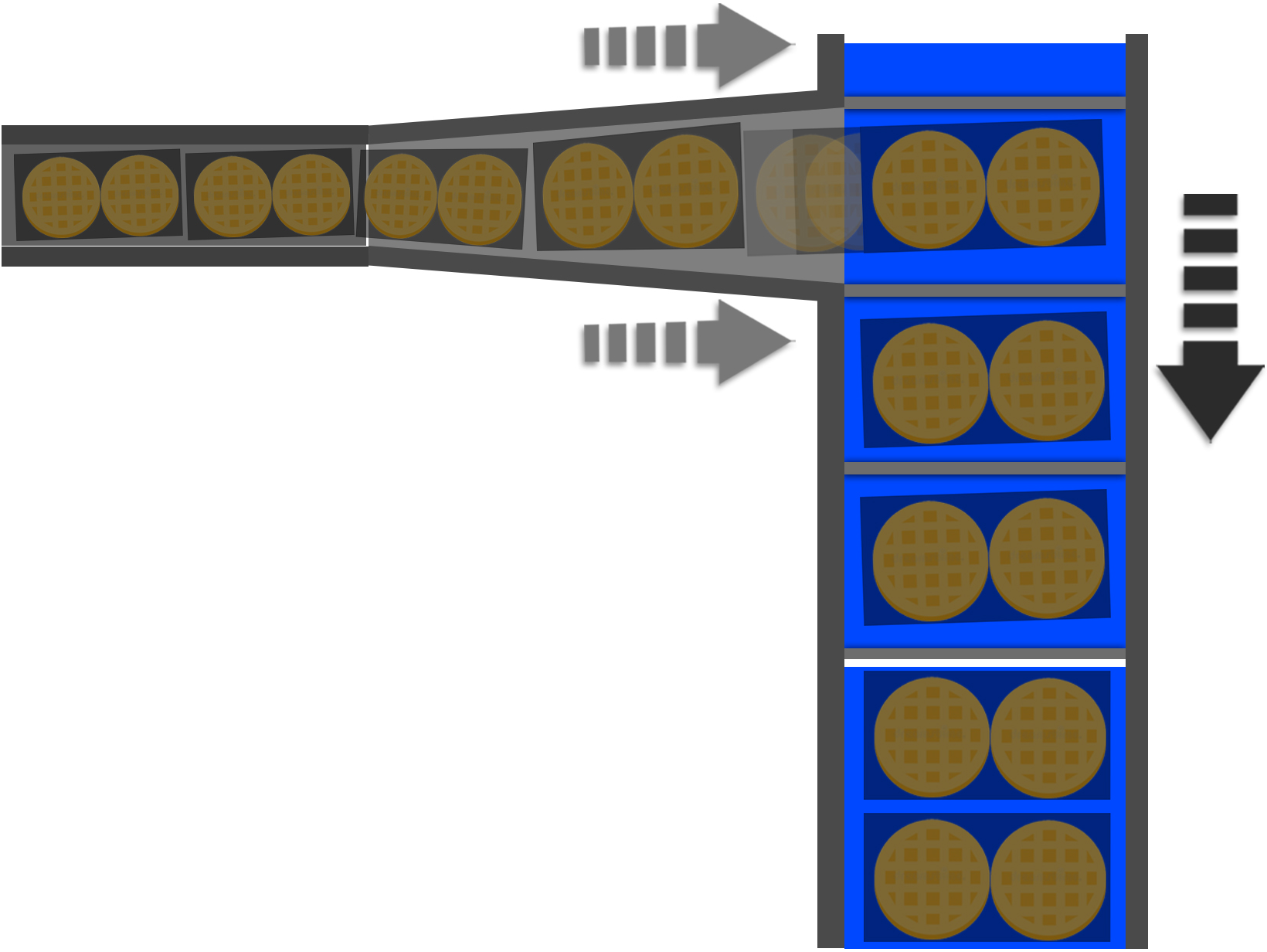
Why Traditional Solutions are Complex and Costly
Each conveyor required for this process takes up space, consumes electrical energy, and increases the likelihood of mechanical failure. There is also wasted time when transfering product from one conveyor line to the next.
According to a representative from Rossi North America, a gear motor and gearbox manufacturer, conveying equipment can consume up to 50% of a facility’s energy usage.
That staggering statistic begins to make sense when you consider the number of motors and gears traditionally used for something as simple as skew correction.
Mechanical failure is possibly just as much, if not more, of a concern. Unplanned maintenance not only carries an expense for replacing parts, but also for downtime.
How To Simplify The Process
Skew correction shouldn’t be complicated, and the One Motion™ Multi-Drive™ dramatically simplifies the process.
Rather than using multiple conveyors, the Twin version of the Multi-Drive™ runs 2 belts on a single shaft or pulley. Because each belt is independently controlled, encoders can be used to determine how the product is skewed and and increase the belt speed of one side to twist the product into the proper position.
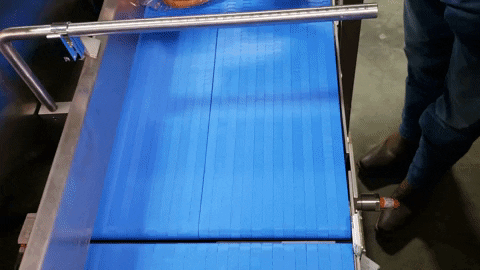
One Motion™ products are already 50+% more energy efficient than gear driven systems. Now, factor in that the Multi-Drive™ replaces the need for multiple conveying systems, and you have an impressive increase in the efficiency of your process.
More than efficiency, you also have the space savings, improved speed (no wasted time passing from one conveyor to another), and a more reliable system that is gearless and uses far less machinery.