Mag-Drive vs Servo Motors
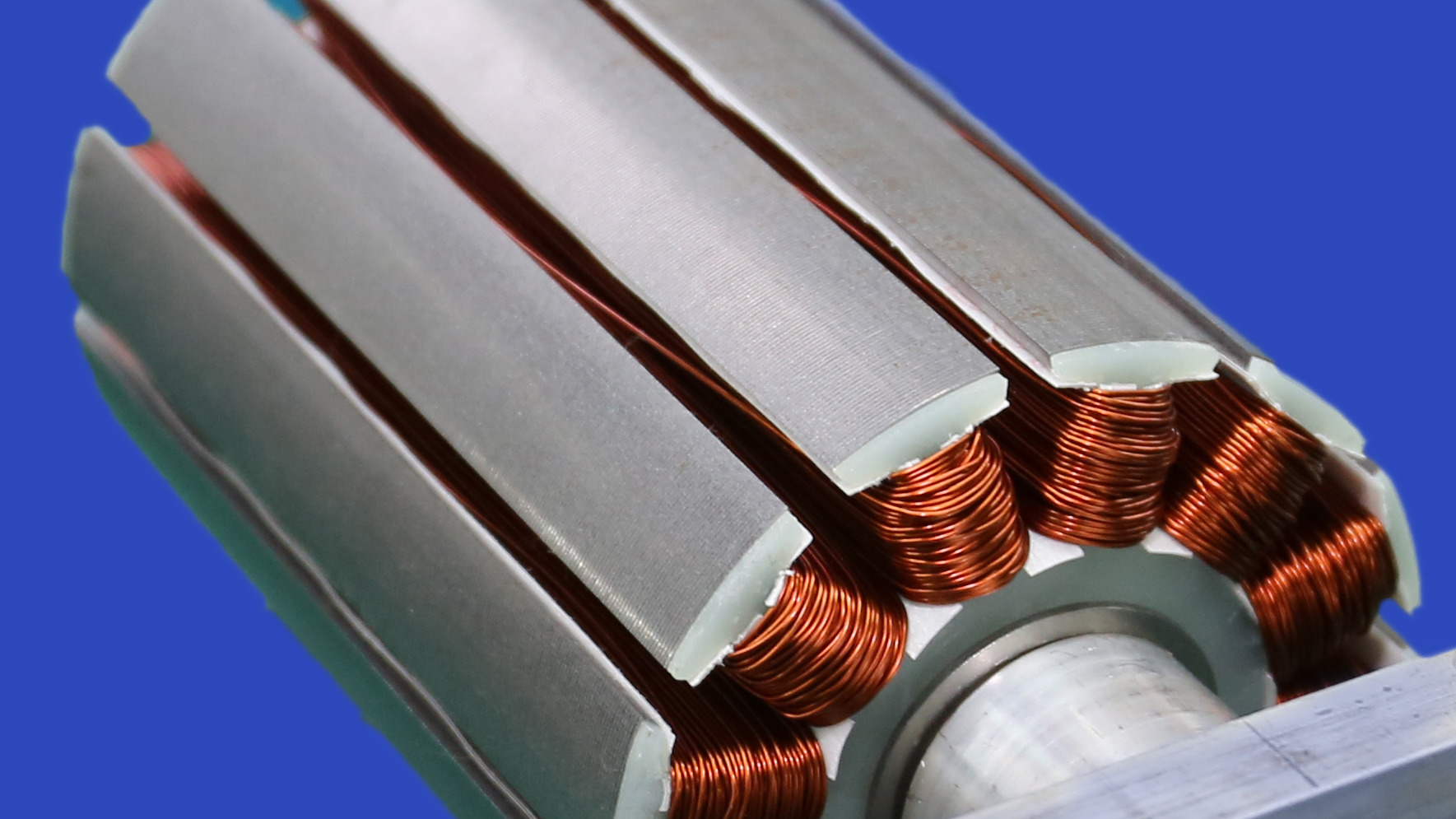
A commonly received question is how the mag-drive compares to a servo motor. While there are some similarities, there are some critical differences which are important to know.
The first on our list is that the mag-drive was designed for the packaging industry. Servo motors were designed to solve other problems.
The mag-drive has fewer mechanical parts than conventional motors, which reduces associated losses, maintenance, and cost. It uses an electromagnetic field created by a stationary part in the center and exerts a force on an array of magnets on the outer shell to create rotation. The result is high mechanical power and torque which can be operated with varying speed and direction.
A servo motor uses mechanical parts with a combination of stator and rotor for its operation. It requires a high level of maintenance, troubleshooting, and repairs.
Cost Effective
The mag-drive is designed using a high array of specially cut magnets. This proprietary design allows for precision timing and indexing within 1/16″. It does not include any mechanical parts such as windings, gearboxes, or couplings that significantly increase a motor’s price.
On the other hand, a servo motor includes all the mechanical parts included in a normally functioning motor. In addition to mechanical parts, the servo motor also includes an encoder and its associated control wirings or cables. The encoder is a sophisticated component that uses electronics to function and provides feedback about the motor characteristics such as rotation, speed, and position. Internal mechanical parts, encoder, and its attached control wirings significantly factor into the price of a servo motor.
Internal Working
The mag-drive uses the magnetic field principle, which converts the electrical energy into EMF. This EMF exerts a force on an array of magnets placed on the outside shell, causing rotary motion of the shell. The speed can be increased or decreased by increasing or decreasing the strength of EMF.
Servo motors use the rotating rotor’s magnetic field to rotate the motor. This contrasts with the mag-drive, where the rotor is not required to create an EMF. A servo motor also requires an encoder for its operation. To properly operate and integrate it with industrial applications, it requires an external amplifier or motion controller called Servo Driver. It is used to operate and control various parameters such as speed, direction, and torque.
Additional Wiring
The mag-drive has a simple wiring structure. It uses a power source to generate EMF inside mag-drive, without additional control cablings. It eliminates routing or repairing control cables in an industrial processing environment.
In addition to power cables, servo motors also have control cables to transmit different electronic signals from the encoder. These signals are used for calculating various motor parameters by an external controller. Servo motors are useless in the absence of these control cables. When these cables become damaged, they must be immediately replaced for their normal operation.
Precise Motor Control
Both the mag-drive and the servo motor can be used in precise motor control applications, but there is a significant advantage to the mag-drive compared to a servo motor. The mag-drive achieves the preciseness due to its unique internal working principle without using any external feedback devices such as an encoder or an external sensor. This eliminates any physical resistance such as friction or electrical losses.
Servo motors were invented for precise motor control applications, but this is only possible with the help of an encoder device that gives feedback on the current motor state. If the encoder becomes faulty or is removed, precise motor control is not possible and will result in an erratic industrial process.
Industrial Process Application
As previously mentioned, the mag-drive was designed with packaging in mind. It is highly reliable and ideal for applications that require extreme cold or hot temperatures or regular washdowns. Because the shell is laser sealed, the internal structure and electrical mechanism is protected from various outside factors such as moisture content. Additionally, the absence of encoders also makes it less vulnerable to these harsh process applications.
The encoder and electronic components of a servo are less resistant to harsh environmental conditions such as high or low temperatures. Additionally, they are also vulnerable to water or moisture content present in the environment.
Operating Mechanism
Mag-drives can be operated by any appropriate Variable Frequency Drive – VFD. It only requires basic VFD programming corresponding to motor specifications. There is no compulsion of using VFD of specific brands or specifications.
On the other hand, servo drive cannot be operated through VFD. Instead, it requires an amplifier or servo controller for its operation. In the absence of a servo driver or if it becomes faulty, the servo motor cannot operate. Additionally, the servo driver must be of specific characteristics and cannot be run through any other servo driver.
The mag-drive offers a simpler, highly reliable design. Built for the packaging industry, One Motion products keep your processes, systems, and machinery running.