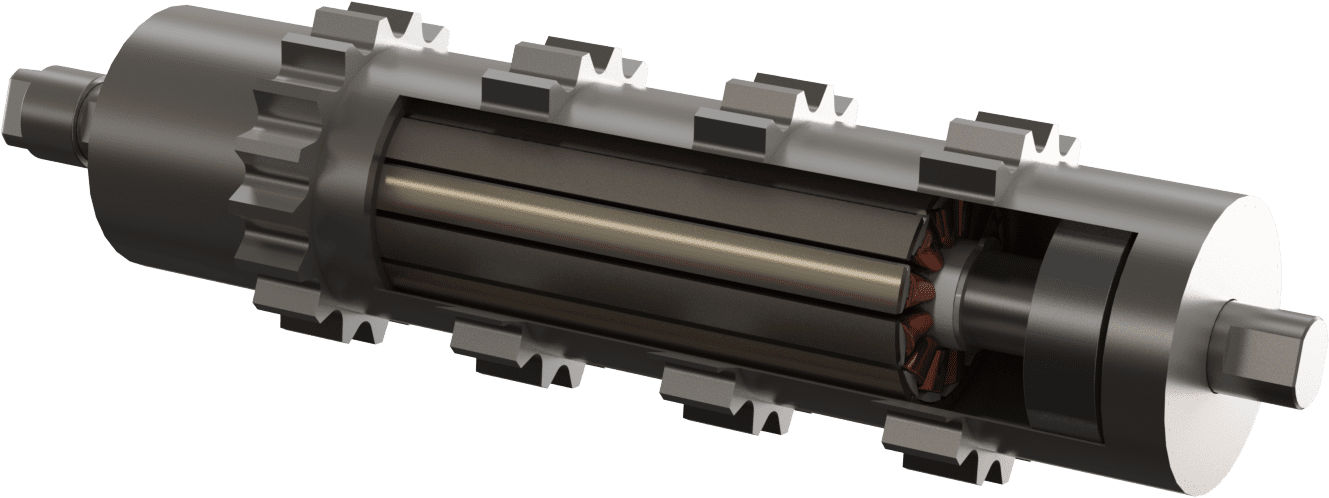
WHAT IS MAGNETIC DIRECT DRIVE TECHNOLOGY?
The term “Mag-Drive” stands for magnetic drive. The name represents our outer-runner design. Using a proprietary design, the mag-drive uses a high pole count to maximize performance. By eliminating gears, electrical power to be used for direct mechanical rotation (watts to torque).
Safe to operate
The Mag-Drive offers a sleek, compact design. Minimal heat is emitted, reducing the risk of an accidental burn. No external components make the mag-drive easy to work-around.
CONFIGURATION TYPES
The Mag-Drive offers 3 configuration types: Powered Pulley, Powered Hub, Powered Multi-Drive.
The pulley is supported on both ends. The hub is supported on one end. The Multi-Drive allows up to 6 pulleys to be independently controlled on a single shaft.
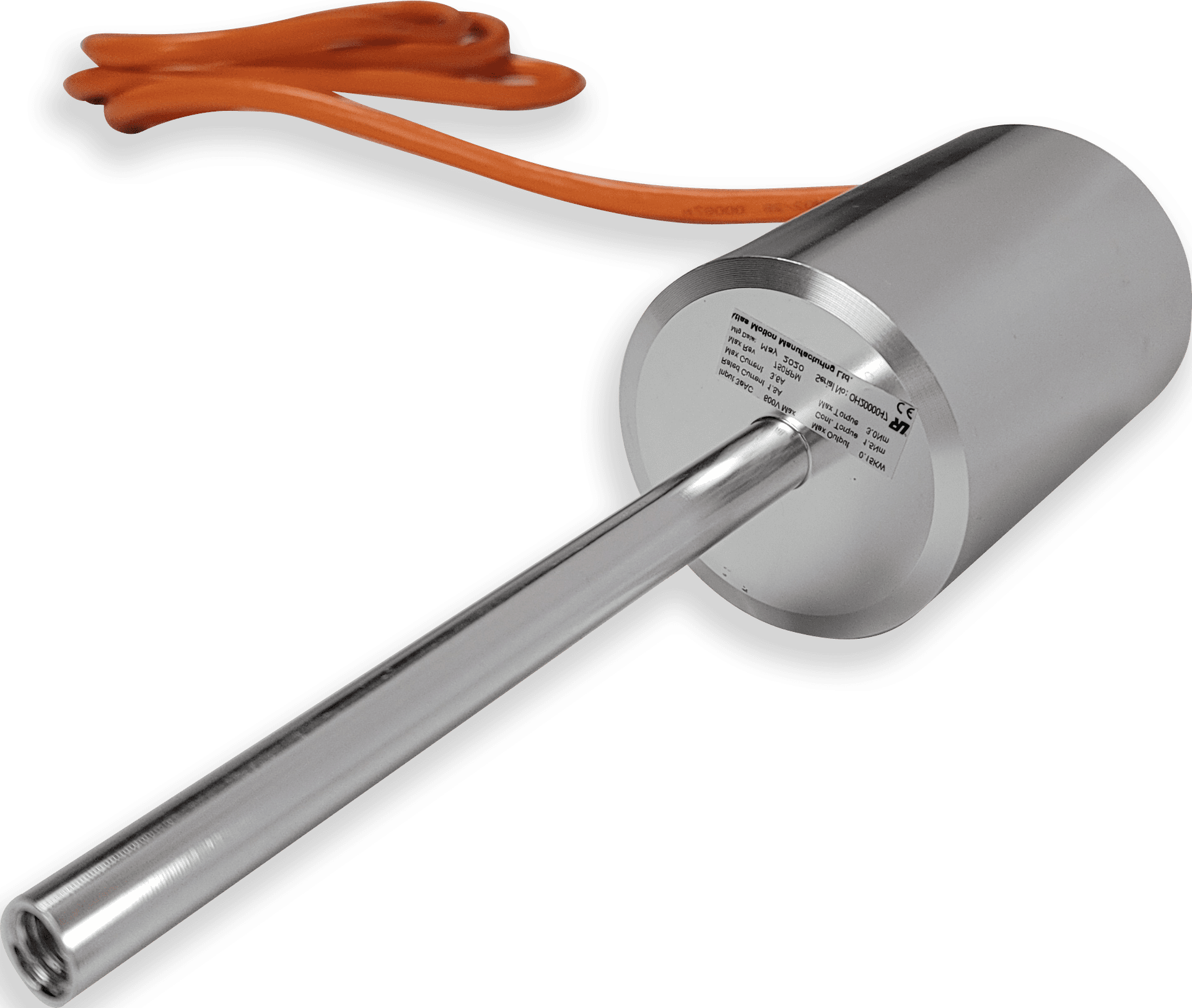
INFINITE DESIGN POSSIBILITES

Custom Shell Profile
- Lagged, Sprocket,
Diameter Range
Your content goes here. Edit or remove this text inline or in the module Content settings. You can also style every aspect of this content in the module Design settings and even apply custom CSS to this text in the module Advanced settings.

Construction
- 316L Stainless Steel
- IP65 or IP69k
- Sealed Enclosure
The Mag-Drive is constructed to endure harsh conditions. The benefit of using so few rotating components is the reliability it provides. With no maintenance being required, the mag-drive has a sealed cap so that no water or other external elements can cause internal damage.
Easy To Operate
- Variable Frequence Drive Operated
The Mag-Drive can be configured to work with practically any VFD that offers permanent magnet mode including Allen Bradley, Yaskawa, Lenze, Emerson and more.
- Quickly Adjust Speed Range From 0 – 500 RPM
Text
- Indexing within 1/16th”
Text

Custom Designed To Fit Application
Text

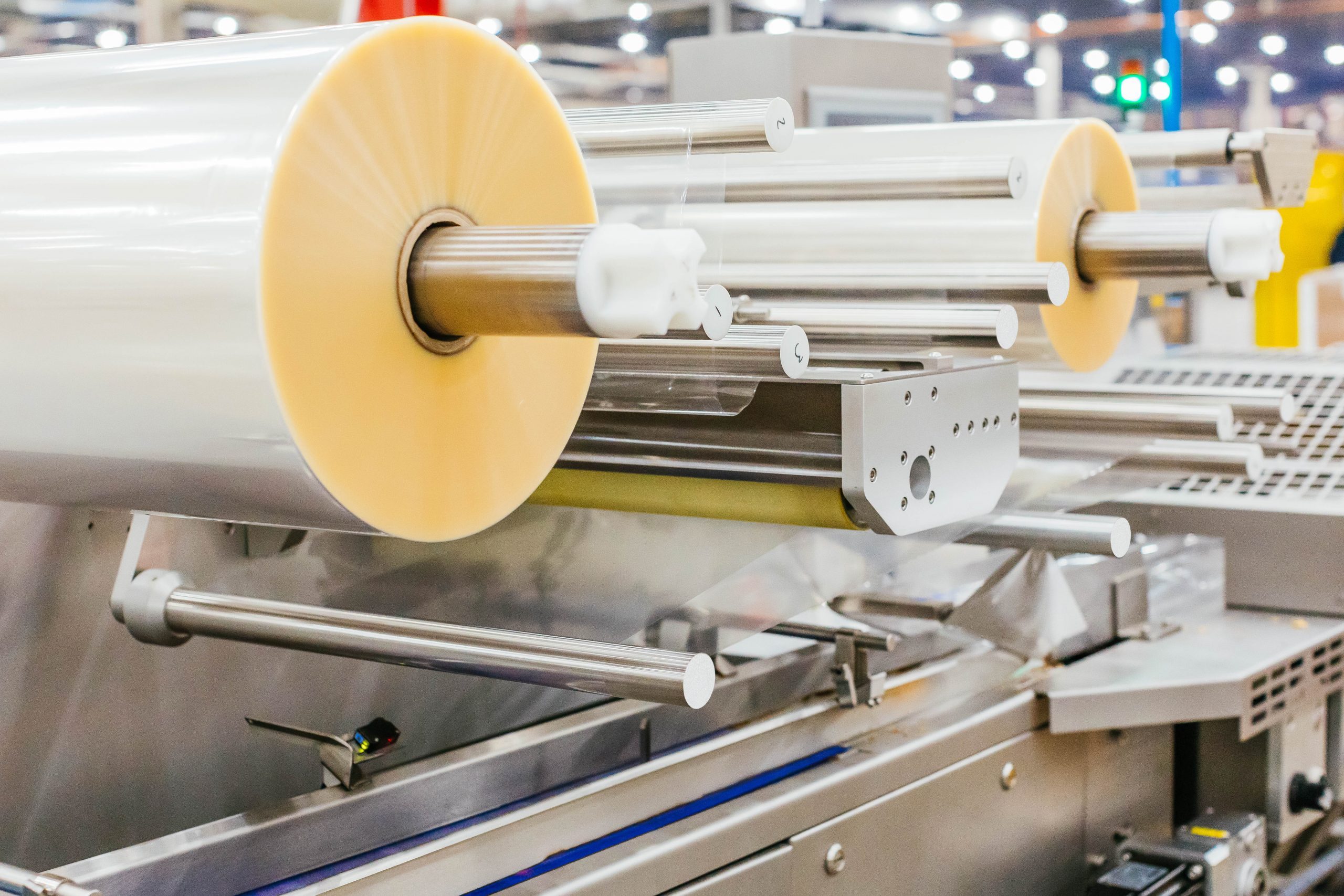
Hygienic Design
The gearless design eliminates the need for lubricants. No oil – no threat of an oil leak.
This makes the Powered Hub an ideal solution for any rotary motion needed above the food line.
Pictured is the Sapphire Flow Wrapper by Atlas.
By embedding One Motion™ direct-drives inside the main components of the wrapper, crevices and cavities that are usually present when designing machinery with conventional motors, servo motors and gearboxes are eliminated.
The sanitary construction of the flow wrapper makes it quick and easy to clean.

PERFORMANCE
One Motion™ products allow precise control over conveyor speeds and timing, and are easy to operate using most popular VFD’s.
• No gearbox = No Gearbox Sizing
• Wide Speed Profile Ranging from 0 – 500
• Constant Torque

EFFICIENCY
Motor-driven systems utilize up to 50% of a facility’s power. One Motion products have been field tested and proven to increase efficiency by up to 55%.
• No loss of energy passing through gears
• One Transfer of Energy
• High Mechanical Power

FOOD SAFETY
No lubricants are used in One Motion™ products, thus no risk of oil leaks.
No motor / gearbox means no harborage areas where food debris likes to hide.
• Cut Shells
• Drives are Sealed Shut
• IP69k Washdown Safe
RESOURCES
CUSTOM DESIGNS
TO FIT YOUR NEEDS
One Motion engineers design, develop and build innovation into
packaging automation products. We can adapt Direct Drive Powered
technology to fit your specific needs.
Projects where One Motion products are be used to improve
production include fin sealing, sausage cutting, mayonnaise slinging, and more.
With our “First Time Right” methodology, our accomplished
engineers move from concept to prototype in a timely manner.
GREEN INITIATIVE
Each Drive Saves
1,000 lbs
of CARBON Annually
CUSTOM DESIGNS
TO FIT YOUR NEEDS
One Motion engineers design, develop and build innovation into
packaging automation products. We can adapt Direct Drive Powered
technology to fit your specific needs.
Projects where One Motion products are be used to improve
production include fin sealing, sausage cutting, mayonnaise slinging, and more.
With our “First Time Right” methodology, our accomplished
engineers move from concept to prototype in a timely manner.
GREEN INITIATIVE
Each Drive Saves
1,000 lbs
of CARBON Annually